Важность использования правильного типа и качества заполнителей невозможно переоценить. Щебень и крупные заполнители обычно занимают от 60% до 75% объема бетона (от 70% до 85% по массе) и сильно влияют на свежеприготовленные и затвердевшие свойства бетона, пропорции смеси и экономичность. Мелкие заполнители (Рис. 5-1) обычно состоят из натурального песка или дробленого камня гранотсева с большинством частиц менее 5 мм (0,2 дюйма). Крупные заполнители (рис. 5-2) состоят из одного песка или комбинации гравия или щебня с частицами преимущественно больше 5 мм (0,2 дюйма) и обычно от 9,5 до 37,5 мм. Несколько месторождений природного заполнителя, называемые карьерным гравием, состоят из
гравия и песка, которые могут быть легко использованы в бетоне
после минимальной обработки. Природный гравий и песок обычно выкапывали или выкапывали из ямы, реки, озера или морского дна.
Щебень получают путем дробления карьерных камней, валунов, булыжников или крупногабаритного гравия. Дробленая с воздушным охлаждением доменного шлака также используется в качестве мелкого или крупного заполнителя.

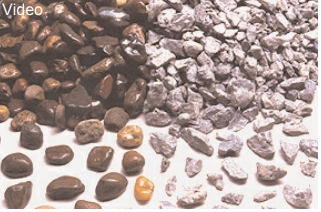
Заполнители обычно промывают и сортируют по типу или фракции. Некоторые различия в типе, качестве, чистоте, классификации, влажности и других свойствах. Почти половина крупных камней, используемых с портландцементом в Северной Америке — это гравий;
большая часть остатка — щебень. Встречающиеся в природе бетонные заполнители представляют собой смесь горных пород и минералов (см. таблицу 5-1). Минерал — это природное твердое вещество с упорядоченной внутренней структурой и химическим составом, который находится в пределах скальных пород, которые классифицируются как магматические, осадочные или метаморфические, в зависимости от происхождения, как правило, состоят из нескольких минералов. Например, гранит содержит кварц, полевой шпат, слюду и несколько других минералов. Большинство известняков состоят из кальцита, доломита и мелкое количество кварца, полевого шпата и глины. Выветривание и эрозия горных пород порождает частицы камня, гравия, песка, ил и глина.
Вторичный бетон или дробленые отходы бетона, является возможным источником заполнителей и экономической реальности,
особенно там, где хороших заполнителей мало. Можно использовать обычное дробильное оборудование. И было разработано оборудование для снижения шума и пыли.
Заполнители должны соответствовать определенным стандартам для
оптимального инженерного использования: они должны быть чистыми, твердыми, прочные, долговечные, частицы без абсорбированных химикатов, глиняных включений и других мелких материалов в количествах, которые могли бы влиять на увлажнение и сцепление цементного теста. Заполнительные частицы, которые являются рыхлыми или способны расщепляться, нежелательны. Материалы, содержащие сколько-нибудь заметное количество
сланцев или других сланцевых пород, мягких и пористых материалов, необходимо избегать. Следует избегать определенных типов материала, поскольку они имеют низкую устойчивость к атмосферным воздействиям и могут вызывать поверхностные дефекты, такие как трещины.
Визуальный осмотр часто раскрывает слабые места в крупных заполнителях. Сервисные записи важны в оценке заполнителей. В отсутствии записей технологом, компоненты должны быть проверены прежде чем они будут использованы в бетоне. Наиболее часто используемый заполнители — песок, гравий, щебень и охлажденный доменный шлак — производят свежесмешанный нормальный вес бетон с плотностью (удельная масса) от 2200 до 2400
кг / м3 (от 140 до 150 фунтов / фут3). Компоненты из сланца,
глины, сланец и шлак (рис. 5-3) используются для производства конструкционного легкого бетона со свежеприготовленной плотностью от 1350 до 1850 кг / м3 (от 90 до 120 фунтов / фут3).
Другие легкие материалы, такие как пемза, керамзит, перлит, вермикулит и диатомит используются для производства
изоляционных легких бетонов плотностью от 250 до 1450 кг / м3 (от 15 до 90 фунтов / фут3). Тяжеловесные материалы, как барит, лимонит, магнетит, ильменит, гематит, железо и сталь штамповки или дробь используются для производства тяжелого бетона и радиационно защитный бетон (ASTM C 637 и C 638).

Для адекватного уплотнения бетона желательно количество воздуха, воды, цемента и мелкого заполнителя (то есть, фракция раствора) должна составлять от 50% до 65% от абсолютного объема (от 45% до 60% по массе). Скругленный заполнитель, такой как гравий, требует немного более низких значений, в то время как дробленый заполнитель требует немного более высоких значений. Хороее
совокупное содержание обычно составляет от 35% до 45% по массе или объем общего совокупного содержания.
Характеристики заполнителей
Оценки
- Фракция — это распределение частиц по размерам агрегата как определяется ситовым анализом (ASTM C 136 или AASHTO). Проектирование и контроль бетонных смесей. Камень и минеральные составляющие в сводные показатели:
- Минералы Магматические породы Метаморфические породы
- Гранит Мрамор кремнезема
- Кварц Сиенит Метакварцит
- Опаловый диоритовый сланец
- Халцедон габбро филлит
- Tridymite Перидотитовый сланец
- Кристобалит Пегматит Амфиболит
- Силикаты вулканического стекла Хорнфелс
- Полевой шпат обсидиан гнейс
- Ферромагнезиальная пемза Серпентинит
- Роговой туф
- Augite Scoria
- Клей Перлит
- Illites Pitchstone
- Каолиньш Фельзит
- Хлориты базальтовые
- монтмориллониты
- Слюда осадочных пород
- Цеолитовый Конгломерат
- Карбонат песчаник
- Кальцит кварцит
- Доломитовая Грейвакка
- Сульфат Субгрейваке
- Гипс Аркосе
- Ангидрит глиняный камень, алевролит,
- Сульфид железа, аргиллит и сланец
- Пирит Карбонаты
- Марказитовый известняк
- Пирротин доломит
- Железооксидный мергель
- Магнетит Мел
- Гематит черт
- Гетит
- lmenite
- лимонит
- Краткие описания см. В «Стандартной описательной номенклатуре
- Составляющие природных минеральных агрегатов »(ASTM C 294). Рис. 5-3. Легкий заполнитель. Керамзит (слева) и расширенный сланец (справа). Диапазон размеров частиц в совокупности иллюстрируется на рис. 5-4. Совокупный размер частиц определяется использованием решетчатых сит с квадратными отверстиями. Семь стандартные сита ASTM C 33 (AASHTO M 6 / M 80) для мелких заполнитель имеет отверстия от 150 до 9,5 мм (№ 100 сито до 38 дюймов.) 13 стандартных сит для грубых заполнителей имеет отверстия от 1,18 до 100 мм (От 0,046 до 4 дюймов). Допуски на размеры отверстий в ситах перечислены в ASTM E 11 (AASHTO M 92).
Фракция (сортирующие размеры) для крупных заполнителей
применяются к количествам совокупного (по массе) в процентах, которые проходят через ассортимент сит (рис. 5-5). Для строительства шоссе, ASTM D 448 (AASHTO M 43) перечисляет те же 13 чисел размера, что и в ASTM C 33 (AASHTO M 6 / M 80) плюс еще шесть более крупных. Мелкий заполнитель или песок имеет только один диапазон размеров частиц для общего строительства и шоссейных работ.

Пределы состава фракции обычно выражаются как процент материала, проходящего через каждое сито. Рис. 5-6
показывает эти пределы для мелкого заполнителя и для наиболее мелкого размера до крупного в совокупности.
Есть несколько причин для указания пределов оценки
и номинальный максимальный совокупный размер. Они влияют на относительные пропорции заполнителя, а также на цемент и воду в составе, обрабатываемость, прокачиваемость, экономичность, пористость, усадка и долговечность бетона. Вариации в оценке может серьезно повлиять на однородность бетона от партии к партии. Очень мелкие пески часто неэкономичны; очень грубый песок и крупнозернистый заполнитель приводит к неработающие смеси. В общем, заполнители, которые не имеют большого дефицита или избытка любого размера и
дать гладкую кривую оценки даст самые удовлетворительные результаты.

Эффект диапазона различных размеров в уменьшении
общего объема пустот между заполнителями иллюстрируется
простым способом, показанным на рис. 5-7. Стакан слева заполнен крупными крупными частицами одинакового размера и формы. Средний стакан наполнен равным объемом мелких агрегатных частиц одинакового размера и формы. И стакан справа заполнен частицами обоих размеров. Ниже каждого стакана находится сосуд с
количество воды, необходимое для заполнения пустот в этом стакане.
Обратите внимание, что когда мензурки заполнены одним размером частиц равного объема, содержание пустот является постоянным, независимо от размера частиц. Когда два совокупных размера
в совокупности содержание пустот уменьшается. Если эта операция
были повторены с несколькими дополнительными размерами, еще
произойдет уменьшение пустот. Потребность в цементной пасте для бетона связана с содержанием пустот комбинированные заполнители.
В первые годы технологии бетона это применялось не часто. Считалось, что наименьший процент пустот (наибольшая плотность заполнителей) была наиболее подходящей для бетона. В то же время были установлены ограничения на количество и размер мельчайших частиц. Теперь известно, что даже на этой ограниченной основе это не лучший вариант для технолога бетона. Тем не менее, производство удовлетворительное, экономичный бетон требует заполнителей с низким содержанием пустот, но не самое низкое.
На самом деле, количество цементного теста требуется в бетон большее, чем объем самих пустот между заполнителем. Это показано на рис. 5-8. Эскиз А представляет собой только крупные заполнители со всеми контактирующими частицами. Эскиз B представляет разгон агрегатов в матрице теста. Количество пасты обязательно больше, чем пустое содержание эскиза А для обеспечения работоспособности бетона. Фактическая сумма зависит от обрабатываемости и связности пасты.

Тонкая совокупная оценка
Требования ASTM C 33 или AASHTO M 6 / M 43 допускают относительно широкий диапазон градаций мелкого заполнителя, но спецификации других организаций иногда более ограничительный. Наиболее желательная мелкозернистая сортировка зависит от типа работы, богатства смеси, а максимального размера крупного заполнителя. В
более жидких смесях, или когда крупные заполнители небольшого размера. Для оценки желательна, которая приближается к максимальному рекомендуемому проценту, проходящему через каждое сито. В целом, если водоцементное соотношение сохраняется
постоянным и выбирается отношение тонкого к грубому заполнителю правильно, широкий диапазон в классификации может использоваться без измеримое влияние на силу. Тем не менее, лучшая экономика иногда будет достигаться путем корректировки бетона смесь в соответствии с градацией местных агрегатов.
Спецификации AASHTO позволяют минимальный проценты (по массе) материала, проходящего 300 мкм (№50) и 150 мкм (№ 100) сит, чтобы уменьшить до 5% и 0% соответственно при условии:
- Наполнители используется в уносимых воздухом бетонах содержащие более 237 кг цемента в кубическом метре (400 фунтов цемента на кубический ярд) и с содержанием воздуха более 3%.
- Агрегат используется в бетоне, содержащем больше чем 297 кг цемента на кубический метр (500 фунтов цемента на кубический ярд), когда бетон не проветрен.
- Одобренный дополнительный цементирующий материал
используется для восполнения недостатка в передаче материала
эти два сита.
Другие требования ASTM C 33 (AASHTO M 6):1.Мелкий заполнитель не должен иметь более 45% сохраняется между любыми двумя последовательными стандартами Сита.
- Модуль крупности должен быть не менее 2,3 более 3,1 и не отличаются более 0,2 от типового значение совокупного источника. Если это значение данный грубый заполнитель максимального размера может варьироваться в зависимости от умеренного диапазона без заметного влияния на цемент и потребность в воде смеси, если доля мелкозернистый заполнитель к общему заполнителю производит бетон — хорошая работоспособность.
- Пропорции смеси должны быть изменены производить работоспособный бетон. С вариациями сложно предвидеть, зачастую экономичнее поддерживать единообразие в производстве и обработке грубых заполнителей, чем для уменьшения вариаций в градации.
- Максимальный размер крупного заполнителя, используемого в бетоне, имеет отношение к экономии бетона. Как правило для небольших заполнителей требуется больше воды и цемента, чем для крупных, из-за увеличения общей площади заполнителя. Вода и цемент, необходимые для спад приблизительно 75 мм (3 дюйма) показан на рис. 5-9 для широкого диапазона крупногабаритных размеров. Рис. 5-9 показывает что для данного водоцементного соотношения количество цемента требуется уменьшается по мере увеличения максимального размера крупного заполнителя. Повышенная стоимость получения или если мелкий заполнитель отклонен, если подходящие корректировки сделаны в пропорциях штрафа и грубая совокупность.
Комбинированная совокупная оценка
Наполнители иногда анализируются с использованием комбинированной градации мелкого и грубого заполнителя вместе, как они существуют в бетонной смеси. Это обеспечивает более тщательный анализ того, как заполнители будут работать в бетоне.
Иногда заполнители среднего размера, около 9,5 мм (3/8в.) размер, не хватает совокупного предложения. В результате чего бетон с высокими усадочными свойствами, с высоким содержанием воды
имеет изъяны — плохая обрабатываемость, плохая прокачиваемость и плохая удобоукладываемость. Сила и долговечность также могут быть затронуты.
Рис. 5-10 иллюстрирует идеальную градацию. Однако, идеальной градации не существует в этой области, но мы можем попробовать подойти к нему. Если проблемы развиваются из-за плохой градации, альтернативные агрегаты, смешивание или специальные скрининг существующих агрегатов, следует рассмотреть.
Комбинированные градации могут быть использованы для лучшего контроля обрабатываемость, прокачиваемость, усадка и другие свойства бетона Абрамс (1918) и Шилстоун (1990) демонстрируют преимущества комбинированного агрегированного анализа:
• С постоянным содержанием цемента и постоянной консистенцией, существует оптимум для каждой комбинации заполнителей, которые будут производить наиболее эффективное водное соотношение цемента и высокая прочность
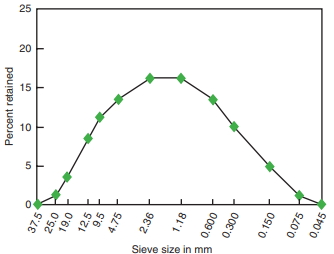
• Оптимальная смесь имеет наименьшие помехи от частиц и лучше всего реагирует на высокие частоты, высокие амплитудный вибратор.
Однако эта оптимальная смесь не может быть использована для
всей конструкции из-за различий в размещении и отделке, потребности и доступности. Крауч (2000) нашел в своих исследованиях на уносимых воздухом бетонах, что водоцементное соотношение может быть уменьшено более чем на 8% при использовании совокупно более широкого диапазона фракций заполнителя. Shilstone (1990) также анализирует совокупную градацию по грубости и факторам работоспособности для улучшения
совокупной фракции.
Разрывные заполнители
В заполненных зазорах заполнителей определенные размеры частиц намеренно принибрегаются. Для монолитного бетона типичные заполненные пустотами заполнители состоят только из одного крупного размера. Агрегировать со всеми частицами тонкого заполнителя, способного пройти через пустоты в уплотненной крупной совокупности. Разрывные смеси используются в архитектурном бетоне для получения однородных текстур в отделках с открытым заполнителем. Они также могут использоваться в обычном структурном бетоне, потому что возможных улучшений в некоторых конкретных свойствах, и разрешить использовать локальные совокупные фракции.
Для агрегата 19 мм (3⁄4 дюйма) максимальный размер от 4,75 мм до 9,5 мм (№ 4 до 3/8 дюймов.) Частицы могут быть опущены, не делая бетон чрезмерно резким или способным на сегрегацию. В случае 37,5 мм (11
In2 в.) Совокупный, обычно 4,75 мм до 19 мм (№ 4 до 3
⁄4 дюйма) размеры опущено.
Необходимо соблюдать осторожность при выборе процента фракции агрегировать в градиентную смесь. Неправильный выбор может в результате превратить бетон, который может отделиться или иметь соты из-за избытка крупного заполнителя. Также бетон с избытком мелкого заполнителя может иметь высокую водную способность приводит к низкой плотности бетона. Мелкий заполнитель обычно составляет от 25% до 35% от общего объема заполнителя. Меньший процент используется с округленными заполнителями и
выше с измельченным материалом. Для гладкой формы необходим, несколько более высокий процент мелкого заполнителя до
общей совокупности может быть использована, чем для открытой совокупности при отделке, но оба используют более мелкое совокупное содержание, чем непрерывно градуированные смеси. Мелкий совокупный контент также зависит от содержания цемента, типа заполнителя и технологичности.
Пористость обычно требуется для работоспособности, поскольку смеси с низкой степенью просачивания и щелей используют низкий процент мелкодисперсного наполнителя и производят жесткие смеси без увлечения воздуха.
Разделение щелейных смесей должно быть предотвращено ограничивая спад до минимального значения. Это может варьироваться от нуля до 75 мм (до 3 дюйма) в зависимости от толщины сечения, количество армирования и высота отливки. Также необходим строгий контроль за градацией и содержанием воды, поскольку может вызвать сегрегацию. Если требуется жесткая смесь, заполненные зазором щебень может давать более высокую прочность, чем обычные заполнители, используемые с сопоставимым содержанием цемента. Из-за их малых объемов мелкого заполнителя и низкого водоцементного отношения, смеси с градиентными зазорами могут считаться неработоспособным для некоторых монолитных конструкций. Однако при правильном распределении эти бетоны легко уплотняются вибрацией.
Форма частиц и текстура поверхности
Форма частиц и текстура поверхности щебня повлияет на свойства свежеприготовленного бетона более, чем свойства затвердевшего бетона. Шероховатый, угловатый, вытянутые частицы требуют больше воды для производства работоспособного бетона, чем делать гладкие, округлые, компактные заполнители. Следовательно, агрегатные частицы. Которые угловые лещадные требуют больше цемента для поддержания того же водоцементного соотношения. Однако, с удовлетворительной градацией, оба дробленые и недробленые щебни (из одного типа породы) обычно дают одинаковую силу для того же цементного фактора. Угловые или плохо оцененные щебни также могут быть более сложным для прокачки.
Связь между цементной пастой и данным заполнителем обычно увеличивается по мере того, как частицы изменяются от гладких
и округлых, до грубых и угловатых. Это увеличение связи соображение при выборе заполнителей для бетона, где прочность на изгиб важна или где высока прочность на сжатие необходима.
Пустое содержимое уплотненного мелкого или грубого заполнителя
может использоваться как показатель различий в форме и
текстуре щебня одной и той же марки. Смешивание в воде и цементе, как правило, возрастает с увеличением содержания пустот. Пустоты между заполненными частицами увеличиваются с угловатостью щебней.
Щебень должен быть относительно свободным от плоских и удлиненных частиц. Частица называется плоской и вытянутой (лещадной) , когда отношение длины к толщине превышает указанное значение. ASTM D 3398 обеспечивает косвенный
метод определения индекса частиц как общей меры формы или текстуры частиц, в то время как ASTM C 295 предусматривает процедуры петрографической экспертизы щебня.
Плоские и удлиненные частицы заполнителя должны избегать или, по крайней мере, ограничивать до 15% от общей массы щебня. Это требование одинаково важно для грубых и для измельченного мелкого заполнителя. Так как мелкий заполнитель при дроблении камня часто содержит плоские и вытянутые частицы. Такие щебневые частицы требуют увеличения смешивания с водой и, следовательно, может повлиять на прочность бетона, особенно при изгибе, если водоцементное соотношение не регулируется.
Доступен ряд автоматизированных тестовых машин для быстрого определения гранулометрического состава щебня. Разработанный, чтобы обеспечить более быструю альтернативу стандартному размеру сита, эти машины захвата и анализировать цифровые изображения агрегатных частиц для определения градации. На рис. 5-11 показан, который измеряет размер и форму совокупности с помощью камер линейного сканирования, в которых построены двумерные изображения. Из серии линейных изображений. Другие машины используют матрицы матрицы для захвата двумерных снимков падающего щебня. Маерц и Люшер (2001) разработали
динамическая система визуализации прототипа, которая обеспечивает частицам информация о размере и форме с помощью миниконвейера, система для показа отдельных фрагментов после двух ортогонально ориентированных синхронизированных камер.
Насыпная плотность (единичный удельный вес) и пустоты
Насыпной вес или удельный вес заполнителя — масса или масса заполнителя, необходимого для заполнения контейнера указанного объема единицы. Объем, указанный здесь которые заняты как совокупности и пустоты между агрегатные частицы.
Приблизительная объемная плотность заполнителя, обычно используемого в бетоне с нормальным весом, колеблется от примерно
От 1200 до 1750 кг / м3 (от 75 до 110 фунтов / фут3). Содержание пустот
между частицами влияет на требования к пасте при проектировании смеси. Содержание пустот варьируется от 30% до 45% для крупных заполнителей и от 40% до 50% для мелкого песка или гранитного отсева. Угловатость увеличивает содержание пустот, в то время как
большие размеры хорошо классифицированного заполнителя и улучшенная классификация уменьшают содержание пустот (рис. 5-7). Методы определения насыпной плотности заполнителей и пустот
приведены в ASTM C 29 (AASHTO T 19). В этих стандартах описаны три метода для заполнителя в контейнере в зависимости от максимального размера совокупности.
Относительная плотность (удельная масса)
Относительная плотность (удельный вес) заполнителя является
отношением его массы к массе равно абсолютному объему воды. Используется в некоторых расчетах для дозирования и контроля смеси, такие как объем, занимаемый щебнем в абсолютном объеме методом смешения. Обычно он не используется как показатель совокупности качества, хотя некоторые пористые заполнители, которые демонстрируют ускоренное разрушение при замерзании-оттаивании, имеют низкий удельный вес. Большинство природных щебней имеют относительную плотность между 2,4 и 2,9 с соответствующей частицей (массой) плотности 2400 и 2900 кг / м3 (150 и 181 фунт / фут3).
Методы испытаний для определения относительной плотности для
грубых и мелких заполнителей описаны в ASTM C 127 (AASHTO T 85) и ASTM C 128 (AASHTO T 84), соответственно. Относительная плотность заполнителя может быть определена по шкале Ovendry или насыщенной поверхностно-сухой (SSD) основы. Как овендри, так и насыщенный поверхностно-сухой метод плотности могут быть использованы при дозировании бетонной смеси. Агрегаты Овендри не содержат каких-либо поглощенная или свободная вода. Их сушат в духовке до постоянного веса. Насыщенные поверхностно-сухие агрегаты какие поры в каждой частице заполнителя заполнены
вода, но на поверхности частиц нет избытка воды.
Плотность
Плотность щебневых частиц, используемых в расчетах дозирования смеси (без учета пустот между частицами), определяется путем умножения относительной плотности (удельный вес) совокупного умноженного на плотность вода. Приблизительное значение 1000 кг / м3 (62,4 фунт / фут3) часто используется для плотности воды. Плотность заполнителя, наряду с более точными значениями плотности воды, представлены в ASTM C 127 (AASHTO T 85) и ASTM
С 128 (AASHTO T 84). Большинство природных щебней имеют
плотность частиц от 2400 до 2900 кг / м3 (150 и 181 фунт / фут3).
Абсорбция и поверхностная влажность
Поглощение и поверхностная влажность заполнителей должны
быть определено в соответствии с ASTM C 70, C 127, C 128 и C 566 (AASHTO T 255), так что общее содержание воды в бетоне можно контролировать и корректировать вес партии определяется. Внутренняя структура частиц заполнителей состоит из твердого вещества и пустот, которые могут или не могут содержать воду.
Условия влажности агрегатов показаны в Рис. 5-12. Они обозначены как:
, Овендри — полностью абсорбирующий
- Воздух сухой — сухой на поверхности частиц, но содержащий
некоторая внутренняя влажность, таким образом, все еще немного впитывающая - Насыщенная поверхность сухая — не впитывает воду ни от того, чтобы вносить воду в бетонную смесь
- Влажный или влажный — содержащий избыток влаги на поверхность (свободная вода)
Количество воды, добавленной в бетонную партию — завод должен быть отрегулирован в соответствии с условиями влажности заполнителей, чтобы точно удовлетворить потребность в воде при приготовлении смеси. Если содержание воды в бетонной смеси не поддерживается постоянной, водоцементное соотношение варьируются от партии к партии, вызывая другие свойства, такие как
прочность на сжатие и обрабатываемость варьируются отпартия к парти.
Крупный и мелкий заполнитель, как правило, будет иметь уровни поглощения (содержание влаги) в диапазоне 0,2%.
до 4% и от 0,2% до 2% соответственно. Содержание свободной воды будет обычно колеблется от 0,5% до 2% для крупного заполнителя и 2% до 6% для мелкого заполнителя. Максимальное содержание воды
в грубом заполнителе обычно меньше, чем мелкого песка. Самые мелкие агрегаты могут поддерживать максимумальное
влагосодержание от 3 до 8%, в то время как грубая агрегаты могут поддерживать только около 1% до 6%
Заполнение: Набухание — это увеличение общего объема влаги
мелкого заполнитель по той же массе сухой. Поверхностное натяжение во влага удерживает частицы друг от друга, вызывая увеличение в объеме. Ссыпка мелкого заполнителя (например, песка)
происходит, когда он сгребен или иным образом перемещен во влажное условие, даже если оно было полностью консолидировано заранее. Рис. 5-13 иллюстрирует, как количество наполнения мелкого заполнителя зависит от содержания влаги и состава. Рис. 5-14 показывает аналогичную информацию с точки зрения веса для конкретного мелкого заполнителя. Поскольку большинство мелких заполнителей доставляются во влажном состоянии, могут существовать большие различия в количествах партии, если дозировка производится по объему. По этой причине, хорошая практика давно одобрила взвешивание совокупности и корректировку для содержания влаги при дозировании бетона.
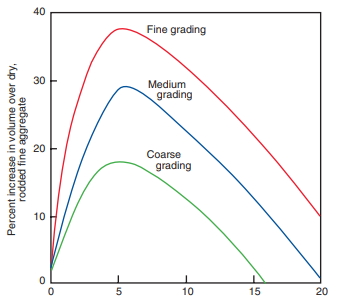
Стойкость к замерзанию и оттаиванию
Морозостойкость заполнителя, важная характеристика для наружного бетона, связана с его пористостью,
поглощением, проницаемость и структурой пор. Совокупность частиц может поглощать так много воды (до критического насыщения), что она не может выдержать расширение и гидравлическое давление, возникающее при замерзании воды. Если присутствует достаточное количество таких частиц, в результатом может быть расширение совокупности и возможное распад бетона. Если одна проблемная частица находится вблизи поверхности бетона, это может вызвать всплывающее окно. Которые разбиваются вне бетонной поверхности. Частица-нарушитель или его часть обычно находятся в нижней части пустоты. Как правило, это крупные, а не мелкие частицы заполнителей с более высокими значениями пористости и порами среднего размера (0,1 до 5 мкм), которые легко насыщаются и вызывают разрушение бетона и выпадение. Большие поры обычно не насыщаются и не вызывают конкретное разрушение, и вода в
очень мелкие поры не могут легко замерзнуть.
При любой скорости замерзания может быть критический размер частиц, выше которого частица потерпит неудачу, если замерзнет, когда критически насыщенный. Этот критический размер зависит от скорости замерзания и пористость, проницаемость и прочность на разрыв частицы. Для мелкозернистых заполнителей с низкой проницаемостью (например, чертов) критический размер частиц может быть в пределах нормальных размеров агрегатов. Это выше для крупнозернистые материалы или материалы с капиллярными системами прервана многочисленными макропорами (пустоты слишком велики, чтобы удерживать влагу капиллярным действием). Для этих агрегатов критический размер частиц может быть достаточно большим, чтобы не иметь следствие, даже если поглощение может быть высоким. Если потенциально уязвимые агрегаты используются в бетоне подвергаются периодической сушке во время эксплуатации, они могут никогда не становиться достаточно насыщенным, чтобы вызвать неудачу.
Растрескивание бетонных покрытий, вызванное разрушением морозостойкого заполнителя в бетоне называется D-крекинг. Этот тип растрескивания наблюдается на некоторых тротуарах после трех или более лет службы. D-треснувший бетон напоминает поврежденный морозом бетон, вызванный износом бетона. Близко расположенные трещины, параллельные поперечному и продольные швы, которые впоследствии размножаются наружу от стыки к центру панели тротуара (рис. 5-15). D-растрескивание является функцией свойств пор некоторых типов наполнителей частиц и среды, в которой
тротуар размещен. Из-за естественного накопления
воды под тротуарами в основании и основаниях, в совокупности может в конечном итоге стать насыщенной. Затем с циклами замораживания и оттаивания, растрескивания бетона начинается в насыщенном заполнителе (рис. 5-16) внизу плиты и прогрессирует вверх, пока не достигнет поверхности износа. Эта проблема может быть уменьшена либо выбор агрегатов, которые лучше работают при замораживании-оттаивании циклы или, где должны использоваться предельные агрегаты, уменьшение максимального размера частиц. Также установка эффективные дренажные системы для отвода свободной воды из-под тротуара может быть полезно

Показатели агрегатов под воздействием замораживания и оттаивание можно оценить двумя способами: (1) прошлые результаты в полевых условиях и (2) лабораторные испытания на морозостойкость бетонных образцов. Если агрегаты из того же источника ранее оказал удовлетворительные показатели
при использовании в бетоне они могут считаться подходящими.
В этих испытаниях конкретные образцы, сделанные с рассматриваемой совокупности подвергнуты чередующимся циклам замерзания и оттаивания в воде. Ухудшение измеряется (1) уменьшением динамического модуля упругости, (2) линейное расширение, и (3) потеря веса образцов. Ошибка расширения
критерий 0,035% в 350 циклах замораживания-оттаивания или менее используется рядом государственных департаментов автомобильных дорог, чтобы помочь указать, подвержен ли агрегат D-растрескиванию. Различные типы агрегатов могут влиять на критерии уровни и эмпирические корреляции между лабораторией
заморозка-оттаивание. Полевые записи должны быть сделаны для
выберите правильный критерий (Vogler and Grove 1989).
Спецификации могут требовать, чтобы устойчивость к атмосферным воздействиям демонстрировалась сульфатом натрия или магнием.
сульфатный тест (ASTM C 88 или AASHTO T 104). Тест состоит из ряда циклов погружения для образца в сульфатном растворе; это создает давление через рост кристаллов солей в порах наполнителя к тому, что производится путем замерзания воды. Образец затем сушат и рассчитывают процент потери веса. К сожалению, этот тест иногда вводит в заблуждение. Заполнители, ведущие себя удовлетворительно в тесте, могут производить бетон с низкой морозостойкостью; и наоборот, плохо работающие агрегаты могут производить бетон с достаточным сопротивлением. Это приписывается, хотя бы частично, к тому факту, что агрегаты в тесте
не ограничивается цементной пастой (как это было бы в
конкретные) и механизмы атаки не совпадают в замерзании и оттаивании. Испытание наиболее надежно для слоистых пород с пористыми слоями или слабыми слоями залегания
Дополнительным тестом, который можно использовать для оценки агрегатов на предмет потенциального D-крекинга, является метод быстрого снижения давления. Агрегат помещается в камеру под давлением и давление быстро сбрасывается, вызывая совокупность
с сомнительной системой пор для разрушения (Янссен и Снайдер 1994). Количество трещиноватости относится к потенциал для D-крекинга.
Смачивающие и сушащие свойства
Выветривание из-за смачивания и высыхания также может влиять на
долговечность наполнителя. Расширение и сжатие коэффициенты породы варьируются в зависимости от температуры и влажности состава. Если происходит попеременное смачивание и сушка, и с определенным типом камней это может привести к постоянному увеличению объема конкретной и возможной поломки. Глинянные
комки, чернозем и другие рыхлые частицы могут быстро разлагаться при многократном смачивание и сушке. Также может развиваться
из-за характеристик набухания влаги определенных заполнители, особенно глиняные шарики и сланцы. Пока нет определения этой тенденции имеются специальные тесты.
Сопротивление истиранию и скольжению
Устойчивость к истиранию заполнителя часто используется как
общий показатель его качества. Сопротивление истиранию имеет важное значение, когда заполнитель должен использоваться на
истирание, как в сверхпрочных полах или тротуарах. Низкое сопротивление истиранию заполнителя может увеличить количество
включений в бетоне при смешивании. Следовательно, это может увеличить потребность в воде и потребовать корректировки водоцементного соотношения.
Наиболее распространенным тестом на сопротивление истиранию является испытание на истирание в Лос-Анджелесе (метод Рэтлера), выполненное в соответствии с ASTM C 131 (AASHTO T 96) или ASTM C.
В этом тесте определенное количество заполнителя помещается
в стальном барабане, содержащем стальные шарики, барабан вращается, и процент износа материала измеряется. Спецификации часто устанавливают верхний предел этой потери массы. Тем не менее, сравнение результатов совокупных испытаний на истирание с износостойкостью бетона сделано с той же совокупностью, как правило, не показывают четкой корреляции. Потеря массы из-за удара в трещотку часто столько, сколько это из-за истирания. Износостойкость бетона определен более точно испытаниями на истирание самого бетона.
Чтобы обеспечить хорошее сопротивление скольжению на тротуарах,
содержание кремнистых частиц в тонком заполнителе должно составлять минимум 25%. Для целей спецификации кремнеземная частица содержания считается равным нерастворимому остатку
содержание после обработки в соляной кислоте в стандартных условиях (ASTM D 3042). Из некоторых готовых песков образуются скользкие дорожные покрытия и должны быть исследованы для принятия перед использованием.
Нагрузки и усадка
Прочность заполнителя редко проверяется и обычно не влияет на прочность обычного бетона, так как так же, как прочность пасты и совокупности связи в цементном тесте. Тем не менее, совокупная сила становится важной в высокопрочном бетоне. Совокупные уровни напряжения в бетоне часто намного выше, чем среднее напряжение на все поперечное сечение бетона. Совокупная прочность на растяжение в диапазоне от 2 до 15 МПа (от 300 до 2300 фунтов на квадратный дюйм) и сжимающий силы от 65 до 270 МПа (от 10000 до 40000 фунтов на квадратный дюйм).
Различные типы заполнителей имеют различную сжимаемость, модуль упругости и усадку, связанную с влажностью характеристик, которые могут влиять на те же свойства в бетоне. Агрегаты с высоким поглощением могут иметь высокую усадку при высыхании. Агрегаты кварцевые и полевые шпаты, наряду с известняком, доломитом и гранитом считаются агрегатами с низкой усадкой; в то время как щебень из песчаника, сланца, роговая обманка и граувакка
часто ассоциируется с высокой усадкой в бетоне (рис. 5-17)
Стойкость к кислоте и
Другим агрессивным веществам
Портландцементный бетон долговечен в большинстве природных сред. Однако в обслуживании иногда
подвергается воздействию веществ, которые будут атаковать его.
Большинство кислых растворов будут медленно или быстро разрушать в бетон портландцемент в зависимости от типа и
концентрация кислоты. Некоторые кислоты, такие как щавелевая кислота, являются безвредными. Слабые растворы некоторых кислот имеют незначительные последствия. Хотя кислоты обычно атакуют и вымывают соединения кальция в цементной пасте, они не могут
легко атаковать определенные щебни, такие как кремнистые породы. Известковые заполнители часто легко реагируют с кислотами.
Тем не менее, жертвенный эффект известковых агрегатов часто преимущество по сравнению с кремнистым заполнителем при слабом воздействии кислоты или в областях, где вода не течет. При известковом заполнителе кислота воздействует на весь обнаженный бетонную поверхность равномерно, снижая скорость атаки на пасту
и предотвращение потери агрегатных частиц на поверхности.
Известковые породы также имеют тенденцию нейтрализовать кислоту, особенно в застойных местах. Кислоты также могут обесцвечивать бетон. Кремнистый заполнитель следует избегать, когда присутствуют сильные растворы гидроксида натрия, так как они атакуют этот тип.
Кислотный дождь (часто с рН от 4 до 4,5) может слегка протравить
бетонные поверхности, как правило, не влияющие на производительность бетонных конструкций. Экстремальный кислотный дождь или сильные кислотные условия в воде могут требовать специальных бетонных конструкций или меры предосторожности, особенно в затопленных районах. Непрерывное пополнение в кислоте с pH менее 4 считается очень агрессивным в отношении заглубленного бетона, например, как труба. Бетон постоянно подвергается воздействию жидкостями с pH менее 3 должна быть защищена в аналогично бетону, подвергнутому воздействию разбавленных кислотных растворов.
Природные воды обычно имеют рН более 7 и редко меньше 6. Воды с рН выше 6,5 могут быть агрессивным, если они содержат бикарбонаты. Углекислота растворы с концентрацией от 0,9 до 3 частей на миллион считаются разрушительными для бетона.
Низкое водоцементное отношение, низкая проницаемость и низкое-среднее содержание цемента могут повысить кислотостойкость или коррозионную стойкость бетона. В результате получается низкая проницаемость от низкого водоцементного отношения или использования дыма кремнезема или других пуццоланов, помогают предотвратить коррозию проникая в бетон. Цемент от низкого до умеренного содержимое приводит к снижению доступности для атаки. Использование известковых заполнителей должны быть рассмотрены где указано.
Некоторые кислоты, газы, соли и другие вещества, которые
не упомянутые здесь также могут разрушить бетон.
Кислоты и другие химические вещества, которые сильно атакуют Портленд
следует предотвратить попадание цементобетона
контакт с бетоном с помощью защитных покрытий
(Kerkhoff 2001)
Некоторые кислоты, газы, соли и другие вещества, которые не упомянутые здесь также могут разрушить бетон. Кислоты и другие химические вещества, которые сильно атакуют Портленд цемент следует предотвратить контакт с бетоном с помощью защитных покрытий.
Огнестойкость и тепловые свойства
Огнестойкость и тепловые свойства бетона — проводимость, коэффициент диффузии и коэффициент теплового расширения — в некоторой степени зависят от минеральных составляющих из используемых заполнителей. Изготовлено и естественно встречающиеся легкие заполнители являются более огнестойкими,
чем заполнители нормального веса из-за их изоляционных свойств и высокотемпературная стабильность. Бетон содержащий известковый грубый заполнитель работает лучше под воздействием огня, чем бетон, содержащий кварц или кремнистый заполнитель, такой как гранит или кварцит. На около 590 ° C (1060 ° F), кварц расширяется на 0,85%, вызывая разрушительное расширение (ACI 216 и ACI 221). Коэффициент теплового расширения агрегатов колеблется от 0,55 х 10-6 на ° С до 5 x 10-6 за ° C (1 x 10-6 за ° F до 9 x 10-6 за ° F).
Потенциально вредные материалы
Вредные вещества, которые могут присутствовать в заполнителях
включают органические примеси, ил, глину, сланец, оксид железа, уголь, лигнит и некоторые легкие и мягкие частицы. Кроме того, камни и минералы, такие как некоторые грунты,
напряженный кварц (Buck and Mather 1984) и некоторые доломитовые известняки реагируют с щелочами (см. таблицу 5-7). Гипсовый
и ангидрит может вызвать атаку сульфата. Определенные совокупности, такие как некоторые сланцы, будут вызывать всплывающие при набухании (просто поглощая воду) или замораживая поглощенную воду. Если щебень уже был в использовании и его применяют повторно — то в нем может содержаться земля, такая как чернозем. Это тоже приводит к вспучиванию. Большинство спецификаций ограничивают допустимые количество этих веществ. История исполнения совокупность должна быть определяющим фактором при определении пределов для вредных веществ. Методы испытаний для обнаружения вредные вещества качественно или количественно
перечислены.
Агрегаты потенциально вредны, если они содержат cоединения, как известно, химически реагируют с Портлендом цементобетон и производить любое из следующего:
- (1)
значительные изменения объема пасты, заполнителей или
обе; - (2) вмешательство в нормальную гидратацию
цемент; и - (3) другие вредные побочные продукты.
- Органические примеси могут задерживать схватывание и отверждение бетона, может снизить прирост прочности, а в необычном случаи могут привести к ухудшению. Органические примеси, такие как торф, гумус и органический суглинок могут быть не такими вредными, но следует избегать.
Материалы тоньше, чем сито 75 мкм (№ 200), особенно ил и глина, могут присутствовать в виде рыхлой пыли и могут образовывать покрытие на заполнителях частиц. Даже тонкие покрытия из ила или глины на частицах гравия могут быть вредными, потому что они могут ослабить связь между цементом вставить и агрегировать. Если определенные типы ила или глины присутствуют в чрезмерных количествах, потребности в воде могут значительно увеличить.
Некоторые мелкие заполнители имеют тенденцию к деградированию от измельчения в бетономешалке. Это эффект, который измеряется с помощью ASTM C 1137, может изменить требования по смешиванию воды. Уголь или лигнит, или другие материалы низкой плотности, такие как дерево или волокнистые материалы, в чрезмерных количествах повлияет на долговечность бетона. Если эти примеси встречаются в илу вблизи поверхности они могут распасться, высолы или вызывают пятна. Потенциально вредный черт в крупном заполнителе можно определить с помощью ASTM C 123 (AASHTO T 113).

Мягкие частицы в крупном заполнителе особенно нежелательны, потому что они вызывают выпадение и могут повлиять на долговечность и износостойкость бетона. Если они рыхлые, они могли бы распадаться во время смешивания и тем самым увеличивают количество воды требуемой. Где стойкость к истиранию имеет решающее значение, тестирование может указывать на то, что дальнейшее расследование или другой совокупный источник
гарантировано. Куски глины, присутствующие в бетоне, могут поглощать некоторые из смешивания воды, вызывающее выпадение в затвердевший бетон, и влияет на долговечность и износостойкость. Они также могут распадаться во время смешивания и тем самым увеличивают потребность в воде для смешивания.
Пески могут иногда содержать частицы железа, оксид и сульфид железа, которые приводят к неприглядным пятнам на
открытые бетонные поверхности (рис. 5-19). Агрегат должен соответствовать требованиям по окрашиванию ASTM C 330
(AASHTO M 195) при испытаниях в соответствии с ASTM C 641. Визуально на песчаном карьере Жихарь и совокупные запасы не должны отображаться свидетельство окрашивания.

В качестве дополнительной помощи в выявлении окрашивающих частиц,
заполнитель может быть погружен в известковый раствор. Если окрашивание
частицы присутствуют, сине-зеленый желатиновый осадок сформируется в течение 5-10 минут; это быстро изменится до коричневого цвета при воздействии воздуха и света. Реакция
должно быть завершено в течение 30 минут. Если коричневый желатиновый осадок не образуется, когда подозрительный агрегат помещается в известковую суспензию, есть небольшая вероятность
любая реакция происходит в бетон. Эти тесты должны
потребоваться, когда агрегаты без записи об успешном предварительное использование используются в архитектурном бетоне.
ALKALI-AGGREGATE
REACTIVITY